In a groundbreaking move, Wilson Sporting Goods introduced the Airless Gen1 basketball, a revolutionary addition that aims to redefine sports technology. The high-tech sphere, boasting a state-of-the-art 3D printing process, is not only a marvel in design but also comes in an array of colors. As athletes and enthusiasts eagerly anticipate its impact, the Wilson Airless Gen1 stands as a testament to the progressive future of sports equipment.
The Wilson Airless Gen1 basketball is a marvel of modern engineering. This technique diverges from traditional methods by molding the ball in a seamless construction, enhancing durability and eliminating the need for inflation. Crucially, the airless design solves a perennial problem plaguing traditional balls: air retention. According to Forbes, the extremely limited release, with only 75 balls made, has made it a value of $2,500. Currently, the ball is mostly bought by enthusiastic collectors. It also solves the issue of the ethical process of creating a basketball and replacing it with plastic. The ball can mimic anything from the exact weight to the way it bounces to become almost indistinguishable from an actual basketball. However, the ball is still doubted by many basketball fans and players.
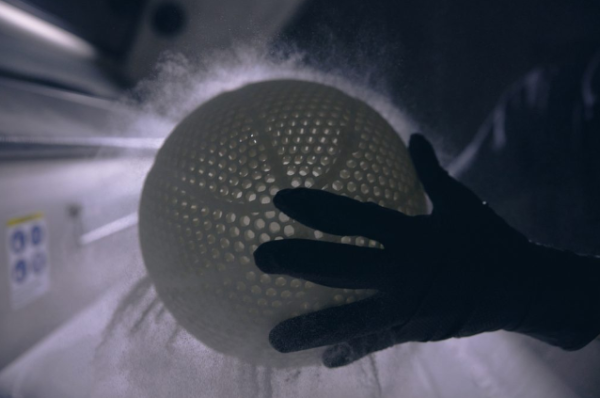
The problem of creating the Wilson Airless Gen1 basketball comes down to the manufacturing time. According to Tyler Webb, a sports YouTuber, when the ball was first created, the company could only make a maximum of one per day. Therefore, when it was released in February, only 75 balls were available. Additionally, another aspect to note is public sentiment. For example, many players express their concerns about growing accustomed to the plastic, rubbery feel rather than the more common leather grip of a standard basketball. However, such issues can be overlooked over time, but for now, the ball might be better for the future.
This innovative approach to basketball design, leveraging the latest in 3D printing technologies, presents a clear path toward more affordable sports equipment without compromising on quality or performance if the company could find a way to manufacture the ball more easily. Additionally, the sustainability advantages of additive manufacturing—such as decreased waste and more efficient use of materials—underscore a growing trend in the sports industry towards environmentally friendly practices, positioning Wilson at the forefront of a greener, more responsible approach to sports equipment production.
In summing up this basketball’s creation, it encapsulates a revolutionary leap in sports technology: a tangible fusion of 3D printing prowess with the raw thrill of basketball. This ball not only represents a visual leap, but also a functional evolution of durability and consistent performance without traditional inflation concerns. It also points to a future where sustainability is interwoven with production as Wilson paves the way for this greener journey.